S'attaquer au casse-tête du carrelage
CATEGORIES :
David A. Short, Zeeco, UK, décrit comment une amélioration de la conception de la tuile radiante traditionnelle utilisée dans les brûleurs de process a été réalisée.
Les tuiles de brûleurs muraux radiants jouent un rôle intrinsèque dans le maintien de la température du four et dans la stabilité et l'efficacité de son fonctionnement. Historiquement, les tuiles de brûleurs muraux radiants étaient fabriquées en quatre pièces à l'aide d'argiles de briques réfractaires cuites au four et moulées à la main, soutenues par des taquets de fixation latéraux externes. Dans les années 1970, la majorité des tuiles de brûleurs muraux radiants étaient fabriquées en deux pièces à l'aide d'un matériau conventionnel en silice d'alumine. Un système de rétention composé de taquets de fixation latéraux et inférieurs était soudé à la plaque de montage avant du brûleur (Figure 1). Cette conception a été adoptée par les principaux fabricants de brûleurs de procédé et s'applique encore aujourd'hui dans la plupart des cas.
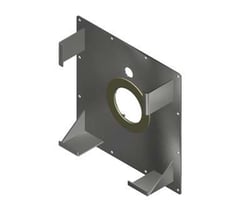
.
Toutefois, cette conception n'est pas sans poser de problèmes. Les principaux problèmes sont le poids de la tuile et les défaillances du système de rétention. Même lorsqu'il est coulé en deux sections, le matériau réfractaire dense est lourd et encombrant à installer, et il nécessite un système d'ancrage et de support étendu, comme le montre la figure 1. Le système de rétention traditionnel permet souvent aux gaz chauds de pénétrer autour de l'espace d'expansion de la tuile du brûleur et, en raison du retrait ou du mouvement du réfractaire adjacent, le gaz qui recircule ou s'échappe non seulement réduit l'efficacité et la stabilité du four, mais augmente la probabilité d'une défaillance prématurée des taquets en raison d'une surchauffe potentielle de la plaque de montage du brûleur ou du boîtier du four.
Pour s'assurer qu'une tuile fonctionne comme prévu, les utilisateurs finaux doivent tenir compte de critères de sélection essentiels pour les matériaux réfractaires. Ces critères sont les suivants
- Température de fonctionnement du four
- Température de la face froide du four
- Chauffage au gaz ou au fioul
- Atmosphère et composition gazeuse oxydantes ou réductrices
- Brûleurs montés sur le toit, les murs ou le sol
- Probabilité d'érosion par les gaz et/ou d'attaque chimique
- Probabilité d'impact direct de la flamme
- Conditions de cyclage thermique.
Une nouvelle conception de tuiles modulaires
Les ingénieurs de Zeeco ont cherché à créer une tuile plus intègre et plus fiable. La conception qui en a résulté, baptisée Zeecolite, est une tuile radiante murale composite d'une seule pièce (figures 2 et 3). Les éléments clés de cette conception comprennent une face chaude résistante à l'érosion et une isolation de secours thermiquement efficace et légère, avec un ancrage sécurisé en acier inoxydable Inconel.
Figure 2. Carreau de brûleur mural radiant composite monobloc Zeecolite - face chaude.
Figure 3. Carreau de brûleur mural radiant composite monobloc Zeecolite - face froide.
La conception modulaire d'une seule pièce utilise un produit moulé à faible teneur en ciment de 1700˚C, à 62 % d'alumine et à faible teneur en oxyde ferrique, comme face chaude, renforcé par des panneaux isolants en fibre céramique (figure 4). Cette conception assure à la fois l'efficacité thermique et la résistance à l'érosion - des critères fondamentaux pour les performances du brûleur et la fiabilité du foyer.
Figure 4. Vue latérale d'une tuile modulaire montrant les panneaux isolants en fibre céramique et le système d'ancrage intégré.
L'assemblage des tuiles est autoportant grâce à un système d'ancrage encastré à quatre points en acier inoxydable Inconel. Le système encastré, entièrement fermé, est utilisé pour fixer le module de tuiles à l'enveloppe du four ou à la plaque de montage du brûleur. Le système d'ancrage est totalement indépendant du réfractaire du four environnant et des composants de combustion du système de brûleur. L'encastrement des ancrages dans la section coulée permet d'éviter les problèmes liés à la fatigue et à l'oxydation du métal (figure 5).
Figure 5. Vue latérale d'un modèle de tuile modulaire montrant les boulons à œil attachés pour manœuvrer la tuile en place.
Derrière la face chaude, le panneau isolant en fibre céramique assure l'efficacité thermique et réduit le poids. Le module de tuiles avec système d'ancrage qui en résulte offre une meilleure efficacité thermique et un poids réduit, besoins fondamentaux des fours modernes d'aujourd'hui.
Répondre aux problèmes de longévité et de démarrage
Les tuiles Zeecolite sont pré-séchées à 360˚C pour assurer l'élimination de l'eau libre et chimique. Ce processus annule le problème courant de fissuration thermique ou de défaillance des tuiles lors des procédures de démarrage. Le système d'ancrage entièrement protégé assure l'intégrité à long terme du système de support et empêche tout mouvement vers l'avant de la tuile par rapport au bec de gaz du brûleur, deux défis de longévité et de fiabilité communs aux conceptions de tuiles traditionnelles. L'ajout de l'isolation en fibre céramique à faible masse améliore l'efficacité thermique, ce qui réduit également les coûts liés à l'énergie pour maintenir le four en fonctionnement dans le respect des spécifications de conception et des objectifs d'efficacité.
Applications
La dalle modulaire d'une seule pièce a été conçue pour être utilisée dans des applications de brûleurs à flamme plate à combustion latérale dans des fours de reformage primaire. La section moulée de la face chaude et l'épaisseur du panneau isolant en fibre céramique peuvent être modifiées en fonction des paramètres particuliers du four ou de l'application. Cette conception convient à toute construction existante ou nouvelle, quelle que soit l'épaisseur des parois ou la composition du réfractaire environnant.
Installation
Le module de tuiles de brûleur est conçu pour être facile à installer, tant pour les nouvelles applications que pour les applications de modernisation. Les ancrages en acier inoxydable encastrés font saillie à travers les panneaux isolants en fibre céramique arrière pour être boulonnés à la plaque de montage extérieure. Pour hisser les modules jusqu'à l'emplacement de montage sur la paroi du four, des boulons à œil qui se vissent sur les boulons d'ancrage sont généralement fournis avec les tuiles. Une fois en place, le système de montage garantit que les ancrages sont capables de suspendre le module de tuiles du brûleur sans aucun mouvement dû au couple gravitationnel, ce qui signifie que le module de tuiles ne transmettra aucune charge ou contrainte importante au système de revêtement environnant. C'est un avantage particulier lorsque des matériaux délicats sont utilisés pour le système de revêtement, comme les modules en fibre céramique réfractaire (FCR). La mise en place du module de tuiles peut être effectuée à l'intérieur ou à l'extérieur, selon que le module est fixé à une plaque de montage du brûleur ou directement à l'enveloppe du four.
Si le motif des boulons d'ancrage ne correspond pas à la disposition existante sur la plaque de montage du four, des trous supplémentaires peuvent être percés dans la plaque de montage en utilisant une planche de gabarit pour localiser les trous ou, alternativement, le module peut être pré-assemblé sur une nouvelle plaque de montage du brûleur. Ce type de module à tuiles est utilisé dans de nombreux fours de reformage à la vapeur et présente des avantages en termes d'efficacité thermique et de longévité.
Étude de cas : Allemagne
Un four avec des brûleurs à tirage naturel à combustion latérale avait une épaisseur de paroi réfractaire de 325 mm à travers la tuile du brûleur.
La tuile originale avait une face chaude de 250 mm d'épaisseur et utilisait un matériau coulé en silicate d'alumine de 1650˚C, avec deux couches de fibres céramiques et de plaques de silicate de calcium ajoutant 75 mm d'épaisseur supplémentaires. La température de la face chaude pouvait atteindre 1200˚C, bien qu'à des fins de comparaison de la conception des tuiles, la température moyenne du foyer utilisée était de 1100˚C. La température de la face froide, dans des conditions ambiantes de 21˚C et sans vent, était de 96˚C avec une perte de chaleur de 936 W/m2.
Le matériau de la face chaude de la nouvelle tuile était composé d'un béton coulé à faible teneur en ciment de 62 % d'alumine 1700˚C et avait une épaisseur de 60 mm entre les âmes d'ancrage et de 160 mm à travers les âmes d'ancrage, avec un support de 165 mm de panneaux isolants en fibre céramique. L'épaisseur totale du module était de 325 mm.
La température moyenne de la face froide des sections coulables, avec les mêmes conditions ambiantes, était de 60˚C avec une perte de chaleur moyenne de 410 W/m2.
L'application de la nouvelle tuile a permis d'améliorer l'efficacité thermique de 56 % et de réduire le poids du module de 79 kg par tuile.
Étude de cas : Autriche
Un four avec des brûleurs à tirage naturel à combustion latérale avait une épaisseur de paroi réfractaire de 293 mm à travers la tuile du brûleur. La température de la face chaude pouvait atteindre 1200˚C, mais à des fins de comparaison de la conception des tuiles, la température moyenne de la chambre de combustion utilisée était de 1100˚C.
La tuile d'origine avait une face chaude de 158 mm et utilisait un coulage en silicate d'alumine de 1650˚C, soutenu par trois couches de panneaux en fibre céramique et silicate de calcium, totalisant donc 135 mm. La température de la face froide, dans des conditions ambiantes de 21˚C et sans vent, était de 77˚C avec une perte de chaleur de 645 W/m2.
Le matériau de la face chaude de la nouvelle tuile était constitué d'un coulage à faible teneur en ciment de 62 % d'alumine 1700˚C et avait une épaisseur de 58 mm entre les âmes d'ancrage et de 158 mm à travers les âmes d'ancrage, doublé de 135 mm de panneaux isolants en fibre céramique. La température moyenne de la face froide des deux sections de béton coulé, dans les mêmes conditions ambiantes, était de 65˚C avec une perte de chaleur moyenne de 468 W/m2.
Par conséquent, une amélioration de 28 % de l'efficacité thermique a été obtenue avec une réduction du poids du module de 38 kg/carreau.
Conclusion
La nouvelle conception des tuiles a réduit les temps d'arrêt des fours et amélioré la longévité des produits. En outre, associée à une meilleure efficacité thermique, son application a permis de réaliser des économies notables sur les budgets d'exploitation et de maintenance.
Figure 6. Brûleurs muraux radiants en fonctionnement dans un four utilisant des tuiles Zeecolite.
Télécharger l'article